DIGITIZING MANUAL VEHICLES
05.06.2024 | naise.eu
BRIDGING THE GAP IN INTRALOGISTICS AUTOMATION
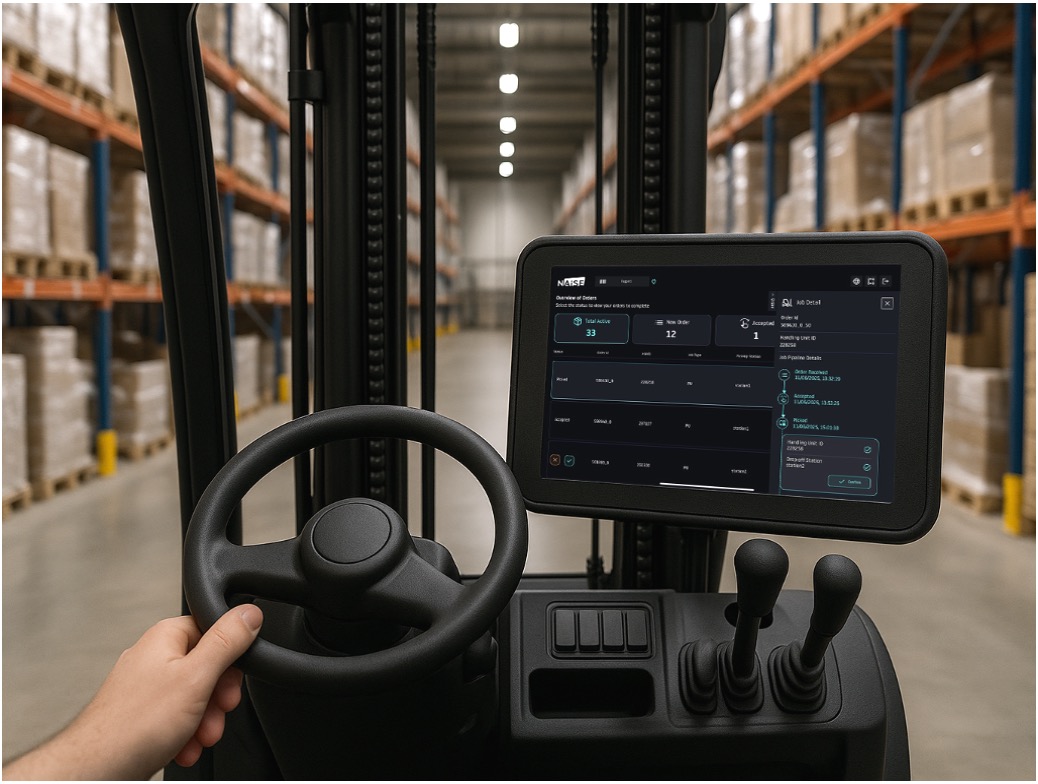
THE CHALLENGE: MANUAL MEETS AUTONOMOUS
Picture a bustling warehouse or production hall, alive with movement and complexity. In one area, manually driven forklifts and tugger trains weave through aisles of goods, operated by experienced workers who rely on instinct, visual cues, and radio communication. The hum of engines and the alertness of human coordination define the rhythm of their work.
In another part of the same facility, mobile robots (AMRs and AGVs) move in a silent, calculated flow—guided by digital maps, sensors, and algorithms. These machines follow optimized paths, avoid collisions automatically, and execute transport tasks with precision and consistency.
Two worlds operating side by side—but not truly together.
This hybrid reality, common in many modern intralogistics and production environments, presents a growing challenge: how to coordinate manual and automated systems without compromising flow or efficiency.
Without a unified digital infrastructure, interactions between human-operated vehicles and autonomous systems often lead to:
- – Route conflicts
- – Unpredictable delays
- – Underutilized equipment
- – And increased risk of accidents
Despite the surge in automation, manual vehicles remain critical—especially in complex or flexible operations where human adaptability is still unmatched. But because these vehicles typically operate in silos, disconnected from central systems, they lack real-time visibility, tracking, and coordination.
The result? Blind spots in the intralogistics flow, increased costs, reduced throughput, and lost potential for optimization.
THE NAiSE SOLUTION: ONE PLATFORM FOR ALL VEHICLES
NAiSE tackles these intralogistics challenges head-on by digitizing manual vehicles within a fully unified framework. The NAiSE Intralogistics Platform stands out as the solution on the market that seamlessly integrates all types of mobile units—whether automated robots like AGVs and AMRs, or manually operated forklifts and tugger trains—into a single intelligent ecosystem.
This integration is powered by real-time connectivity, sophisticated traffic management, and comprehensive digital oversight, ensuring every vehicle operates in perfect harmony. The result is a synchronized fleet where manual and autonomous vehicles coexist without conflicts or bottlenecks, greatly enhancing operational transparency, flexibility, and simplicity.
As the part of this digital transformation lies NAiSE’s cutting-edge Digital Twin technology. This technology creates a live virtual replica of the entire intralogistics environment, reflecting the exact position and status of every forklift, tugger train, and robot in real time. Operators gain unprecedented visibility and control, enabling them to:
-
– Monitor and manage fleet movements continuously
-
– Identify and resolve inefficiencies proactively
-
– Leverage data-driven insights for smarter decision-making
-
– Predict and prevent potential disruptions before they occur
By closing the information gap between manual and automated vehicles, the Digital Twin eliminates blind spots that traditionally hamper intralogistics management. This leads to optimized traffic flow, and increased throughput—all while reducing operational costs.
HOW THE INTEGRATION OF MANUAL VEHICLES WORKS
The integration of manually driven vehicles into the NAiSE Intralogistics Platform follows a structured, step-by-step approach. Each stage is designed to enable seamless coordination, increase efficiency, and support a smooth transition from isolated manual operations to a connected digital ecosystem.
1. Localization & Real-Time Position Tracking
The process begins with precise localization of all manually driven vehicles within the facility. This enables real-time position tracking, laying the foundation for coordinated traffic flow and accurate task assignment.
2. Communication with Forklift Drivers
Forklift operators are equipped with a dedicated user interface (GUI/Terminal), ensuring clear two-way communication with the system. Task notifications, navigation support, and alerts are delivered directly to the driver—bridging the gap between human and system.
3. Cooperation Between Manual and Autonomous Vehicles
The NAiSE platform orchestrates cooperative workflows where mobile robots and manual vehicles operate side by side in shared environments. Dynamic route adjustments and traffic control ensure that both types of vehicles work efficiently without interference.
4. Partial or Full Control of Manual Vehicles
Depending on the integration level and technology of the vehicles (for example flexlog), the platform can exercise partial or full control over manual units. This enables centralized traffic management, collision avoidance, and optimal task scheduling—even for manually operated vehicles.
5. Transport Order Execution & Operational Analytics
Once transport orders are completed, NAiSE automatically captures and analyzes all operational data. This includes route efficiency, task completion times, and interaction patterns—empowering continuous improvement and predictive optimization.
DRIVING THE FUTURE OF LOGISTICS – TOGETHER
In a world where every second counts, and every meter of movement matters, the integration of manually driven vehicles into digital intralogistics systems is no longer a luxury—it’s a necessity. NAiSE transforms traditional intralogistics by removing the boundaries between manned and automated systems, turning fragmented processes into a single, orchestrated flow.
With NAiSE, forklifts and tugger trains are no longer isolated actors. They become intelligent participants in a fully connected ecosystem—visible, manageable, and optimized in real time. Whether you’re taking the first steps toward digitization or expanding an existing automation strategy, NAiSE offers the platform to unify, coordinate, and elevate your operations.