NAiSE SUCCESS STORY: CONTINENTAL REGENSBURG
08.04.2025 | naise.eu
ALL-IN-ONE INTRALOGISTICS CONTROL: FLEET, TRAFFIC & ORDER MANAGER
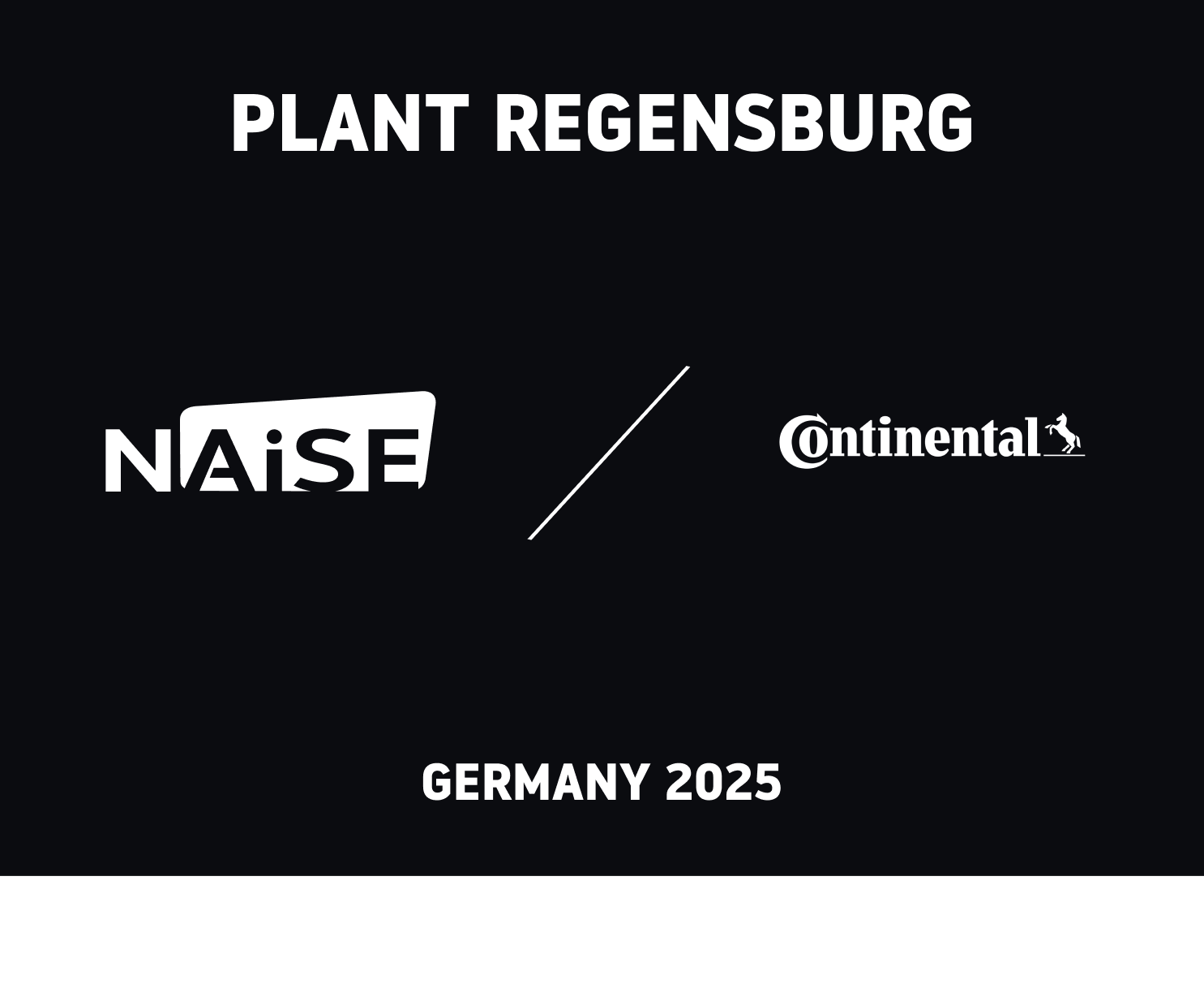
CONTINENTAL REGENSBURG: A PIONEER IN SMART AND SUSTAINABLE MANUFACTURING
Continental’s Regensburg plant stands as one of the largest electronic plants at Continental playing a crucial role in automotive innovation and sustainability. With a workforce of about 4,100 employees, this high-tech location with its production site is a hub for cutting-edge manufacturing, continuously striving for efficiency and operational excellence. Operating within the Continental Business System (CBS), the plant follows a lean approach, emphasizing maximum efficiencies, fast decision-making, and a high level of employee responsibility.
The facility spans two floors, utilizing NAiSE software to coordinate seamless intralogistics across different levels. Within this space, a dedicated area is reserved for high-performance onboard computer manufacturing, where precision and reliability are essential. In such a complex and fast-paced production environment, efficient material flow is critical. The plant relies on dozens of Autonomous Mobile Robots (AMRs) to transport materials and optimize workflows. However, integrating different AMR models from multiple manufacturers into a single, coordinated system posed a major challenge. The lack of centralized intralogistics management led to inefficiencies, congestion, and potential operational risks.
This is where NAiSE stepped in—with its intelligent fleet, traffic and order management solution, enabling seamless collaboration between AGVs and AMRs. By harmonizing robotic movement, preventing conflicts, and optimizing fleet efficiency, NAiSE has redefined intralogistics at Continental Regensburg, setting a new benchmark for smart, automated production.
THE CHALLENGE: MULTI-VENDOR ROBOT INTEGRATION
Ensuring a smooth and efficient intralogistics flow in a highly automated production environment requires seamless coordination between different autonomous mobile robots (AMRs) and automated guided vehicles (AGVs). At Continental Regensburg, this presented a significant challenge due to the variety of robots from multiple manufacturers operating under different software standards.
The plant’s fleet consists of:
- – 61 AMRs managed by the NAiSE Fleet Manager: 55 AMRs from one manufacturer and 6 AMRs from the other manufacturer.
- – Traffic Manager handling both VDA 5050-compliant and non-VDA 5050 transport mobile robots.
Key Implementation Challenges:
- – Multiple Software Standards & Interfaces: Each robot brand had its own proprietary software, requiring significant effort to ensure interoperability and real-time data exchange.
- – Complex Material Pickup & Delivery Processes: The coordination of different loading, unloading, and transportation tasks added another layer of complexity, requiring a solution that could dynamically assign and optimize tasks across different robot types.
- – Real-Time Traffic Optimization: With dozens of robots moving simultaneously across a multi-floor production site, avoiding congestion and optimizing traffic flow in real time was critical to maintaining uninterrupted operations.
To overcome these challenges, Continental Regensburg turned to NAiSE—a cutting-edge intralogistics management solution designed to harmonize multi-vendor AMRs, ensuring a fully integrated, efficient, and intelligent intralogistics system.
ROBOT INTERACTION AND MOVEMENT IN A TIGHT SPACE
At the beginning of the process, robots travel to the warehouse to pick up the required goods for production. They then begin their journey toward the production lines, where the goods will be delivered. What makes this step interesting is the robots’ need to move within a very tight space. This is not a simple linear transport task—robots must navigate narrow aisles where their paths often cross, making it crucial that their movements are continuously coordinated.
As these robots follow their paths, one of the significant challenges they face is encountering each other in these tight spaces. Since the robots are moving along the same route, there’s a high risk of collision if they aren’t synchronized. This is where real-time coordination systems become essential, ensuring that robots can adjust their movements dynamically to avoid accidents and ensure continuous workflow. By using advanced algorithms and NAiSE’s Rules Management, the robots are given movement priorities based on real-time data from the environment, optimizing the flow of materials while maintaining a collision-free zone.
Once the robots begin moving toward the production lines, their task shifts to more precise delivery. They don’t just stop at the edge of the production area; instead, they proceed deep into the production rows, directly reaching production machines and lines. This requires an incredibly high level of precision in movement. The robots need to accurately deliver goods to exact locations within the production system, where even a minor deviation could disrupt the manufacturing process. For this, the robots must continuously adjust their paths, taking into account the dynamic environment, such as moving parts of the machines or changes in the production schedule, which is a common usage of flexible NAiSE solutions. NAiSE’s platform is designed to integrate and manage these processes seamlessly, ensuring that robots are able to operate efficiently without the risk of delay or interruption.
NAISE INTRALOGISTICS PLATFORM: DO IT YOURSELF
To address the complexity of multi-vendor robot integration at Continental Regensburg, NAiSE provided an intelligent intralogistics management solution that seamlessly coordinates different AMR types, optimizes material flow, and ensures conflict-free navigation. The system is composed of three core components: Fleet Manager, Traffic Manager, and Order Manager, each playing a crucial role in harmonizing intralogistics within the plant.
NAiSE Fleet Manager
At Continental Regensburg, where 61 AMRs operate simultaneously, ensuring smooth coordination and optimal utilization of resources has become a top priority. NAiSE Fleet Manager has been deployed as a centralized control system, unifying the operations within a single intelligent platform. NAiSE enables complete control over all AMRs within the plant. This means that you can move stations, nodes, and edges directly within the software in just a few seconds — whenever you need to, and as often as you want.
One of the core challenges in multi-vendor AMR environments is the fragmentation caused by different communication protocols, software interfaces, and navigation strategies. Traditionally, each robot type operates within its ecosystem, leading to inefficiencies such as overlapping tasks, suboptimal route planning, and logistical bottlenecks. The NAiSE Fleet Manager eliminates these barriers by enabling seamless coordination of all AMRs—regardless of manufacturer—through a unified MQTT-based communication interface. This integration allows the system to dynamically assign and monitor tasks in real-time, ensuring continuous synchronization across the fleet.
NAiSE Traffic Manager
As factories become increasingly automated, the seamless coordination of autonomous mobile robots (AMRs) is essential to maintaining efficiency and productivity. At Continental Regensburg, where dozens of AMRs operate simultaneously, ensuring smooth navigation without traffic congestion, delays, or conflicts is a significant challenge. To address this, NAiSE Traffic Manager has been implemented as a real-time, intelligent traffic control system, designed to synchronize all AMRs within the facility, prevent congestion, and optimize material flow.
NAiSE Traffic Manager provides standardized communication between robots from different manufacturers thanks to its rules management functionality that enables robots from different vendors to exchange real-time data and coordinate movements harmoniously. Beyond basic navigation, the Traffic Manager actively analyzes traffic flow across the factory. Through its Traffic Analysis function, operators can identify congestion points, detect inefficiencies, and implement proactive adjustments to avoid bottlenecks.
NAiSE plays a pivotal role in enabling full industrial automation. Given the multiple production and storage levels in the facility and their connection via a lift, NAiSE oversees the lift’s usage. The lift is seamlessly integrated into the NAiSE Intralogistics Platform, and its efficient operation by robots is ensured through NAiSE’s Rules Management. This system provides the necessary movement priorities, optimizing the lift’s use and ensuring smooth and effective logistics operations.
A breakthrough feature of the NAiSE Traffic Manager is its 3D Digital Twin—a real-time, interactive map of the entire production environment. This visualization tool enables operators to monitor every movement within the facility, gain instant insights into potential inefficiencies, and dynamically adjust paths to maintain optimal logistics performance.
NAiSE Order Manager
NAiSE Order Manager has been deployed as an intelligent coordination system, designed to optimize task assignment based on priority, robot availability, and route efficiency. By integrating multiple task sources into a unified system, NAiSE Order Manager ensures that intralogistics operations remain fast, efficient, and adaptable.
One of the most innovative aspects of NAiSE Order Manager is its ability to aggregate and prioritize task requests from various sources:
- – Geofence-Triggers: The system automatically initiates transportation tasks when predefined conditions are met—such as the arrival of goods at a specific location—eliminating manual intervention and accelerating response times.
- – Automated Task Assignment via NodeRED: By leveraging rule-based automation workflows, NAiSE Order Manager can dynamically assign tasks based on real-time logistics needs, ensuring optimal resource utilization.
- – Middleware Integration for AMRs: While automation is key, flexibility remains essential. The system allows manual task input when needed, providing operators with control over custom task assignments and ad-hoc requests.
- – Multi-Source Order Processing: NAiSE Order Manager seamlessly integrates two primary order sources: orders received via MQTT through a dashboard designed by the Regensburg plant and orders received via REST for a specialized solution tailored for AMRs. This dual-input approach ensures smooth coordination and adaptability across different operational environments.
Beyond simple task distribution, NAiSE Order Manager enhances the entire intralogistics workflow by ensuring that every task is executed with precision and efficiency. The system continuously analyzes robot availability, location, and task priority, dynamically adjusting assignments to prevent bottlenecks and optimize material transport. Whether managing material pickups, deliveries, or lift coordination, the system adapts to various logistics processes, ensuring that the right AMR is assigned to the right job at the right time.
One of the key aspects of this use case is the Do-It-Yourself (DIY) concept. Once the NAiSE system was installed and initial workshops and training were conducted, the Continental team became fully autonomous in operating the software. Today, they independently:
- – Add new robots and define their behavior,
- – Create and update zones and rules,
- – Define and dispatch new orders,
- – Design and customize dashboards,
- – Modify stations, nodes, and edges,
- – Adjust traffic and routing logic.
The system is highly flexible, and our collaboration has now reached a stage where Continental simply shares their evolving needs, and our development team continuously enhances the platform—designing specific new features tailored to their operations in Regensburg.
ADVANCED INTRALOGISTICS WITH NAISE
The next phase of development focuses on enhancing system capabilities, expanding integrations, and further refining traffic management processes to ensure seamless, conflict-free material flow.
This will mark another significant step toward a truly vendor-agnostic intralogistics environment, where robots from different manufacturers work together seamlessly. These enhancements will provide a more detailed, real-time digital twin of the production facility, offering improved visualization of AMR movements and congestion points.
With these next steps, Continental Regensburg is reinforcing its commitment to innovation in smart factory logistics. By embracing intelligent automation, multi-vendor fleet management, and advanced traffic analysis, the company is setting new standards for efficiency, adaptability, and seamless material flow in manufacturing environments.