NAiSE CUSTOMER SERVICES
02.04.2025 | naise.eu
SUPPORT FOR CUSTOMIZED AND FULLY INTEGRATED SOLUTIONS
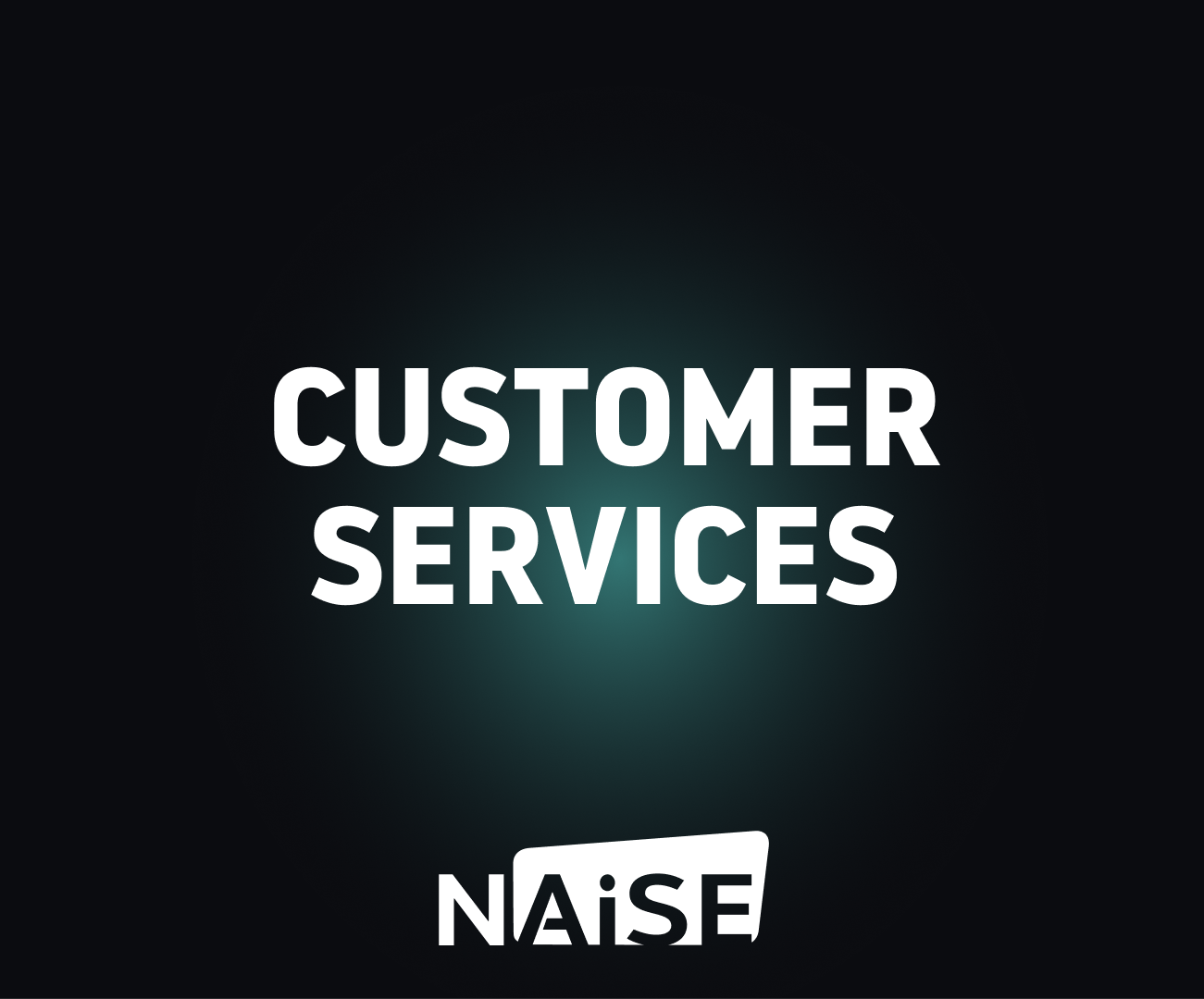
UNLOCK 100% POTENTIAL OF YOUR INTRALOGISTICS
COMPREHENSIVE WORKSHOP
At NAiSE, we ensure that every customer receives proper training before the installation of our software. To guarantee a smooth and effective implementation, our team provides a full-day workshop designed to equip users with the necessary knowledge and skills to operate the NAiSE Intralogistics Platform efficiently.
We offer two specialized workshops tailored to different user needs:
- – Operator Workshop – This intensive training session focuses on teaching users how to operate the NAiSE Intralogistics Platform efficiently. Participants will learn the key functionalities required for daily operations, ensuring seamless system usage.
- – Admin Workshop – Designed for administrators, this workshop covers the basic setup and configuration of the software. It provides insights into system management, user settings, and customization options to optimize performance.
During the workshop, participants will explore a wide range of topics, including: GUI (Graphical User Interface), Log Management, Settings & Configuration, License Information, Graphics & Interfaces, User Management, System Architecture, Map Management, Trackables & Trackables Groups, Trackable Control, Zones and Map Elements, Fire Alarm System, Order Manager & Chained Order Processing, Dashboard Overview, Data Analysis Tools, Forklift UI and Support Ticket System.
By attending this workshop, users gain a deeper understanding of the NAiSE platform, allowing them to fully leverage its capabilities for enhanced intralogistics operations.
3D SCANNING & MAPPING
NAiSE offers precise mapping services through advanced 3D scanning technology, enabling the digitization of physical objects and environments. Our specialized approach to map management allows users to visualize their facility in both 2D and 3D within the NAiSE platform.
For an accurate 3D representation, the entire space must be scanned using a professional 3D scanner. NAiSE provides this service for customers who want a more detailed spatial understanding of their environment. However, this 3D map does not define or impact the software’s core functionalities—it is purely a visualization tool.
Since NAiSE software is based on a DIY approach, customers have full control over their mapping data. They can modify, adjust, and upload new maps at any time, ensuring complete flexibility and adaptability to their operational needs.
SYSTEM INTEGRATION
After the workshop and 3D mapping are completed, the next phase involves defining the use case and integrating the software, which happen simultaneously. Our goal in this phase is to ensure seamless system integration, carried out by our experts in close collaboration with the plant’s technical team, management, and the technology partners involved in the specific use case. We focus on connecting all the different automation components, ensuring that the entire intralogistics operation is fully synchronized and optimized.
In addition to the system integration, we also ensure the synchronization of the NAiSE system with all other systems within the plant. This includes the integration with ERP systems and any other systems connected via MQTT. Achieving this full synchronization across the plant is essential for maximizing operational efficiency and ensuring smooth data flow between all systems. By linking everything together, we ensure that no system operates in isolation, resulting in a more efficient, streamlined process.
If the use case only involves mobile robot transport, the customer can independently perform the system integration. However, if the integration requires NAiSE UWB RTLS installation, our team must be physically present on-site to complete the process. For example, we successfully executed a remote installation in China during the COVID-19 pandemic, showcasing our ability to manage installations even in challenging circumstances.
Moreover, if a customer is using a robot brand that is not yet part of our existing ecosystem, our team works closely with the technical team of the robot manufacturer to perform the necessary integration and testing. This integration and testing process can take place directly at the customer’s plant or at ARENA2036, depending on the project’s needs.
Finally, after the integration, we conduct extensive testing and validation of the entire system to ensure that all components work together smoothly. This ensures that the system is fully optimized, performs as expected, and meets all the requirements set out in the use case definition.
POST-INSTALLATION SUPPORT MODELS
Once the software is installed and the use case is up and running, the concept is designed so that customers only need basic knowledge to operate the platform. Thanks to its user-friendly interface, the NAiSE Intralogistics Platform follows a DIY (Do It Yourself) approach, meaning that customers are empowered to use the solution on their own. NAiSE provides the necessary tools and components, and it’s up to the customer to assemble them into a cohesive and compatible system that meets their quality and quantity needs. The platform offers transparency, flexibility, and simplicity, giving customers the freedom to create solutions tailored to their operations.
However, NAiSE understands that some companies or specific situations may require additional support. In such cases, NAiSE offers a variety of support models to cater to different needs:
- – Basic Support: Monday to Friday, 9 AM to 5 PM.
- – Expanded Support: Monday to Friday, 9 AM to 10 PM.
- – 24/5 Support: Monday to Friday, 12 AM to 12 PM.
- – 24/7 Support: No limitations.
Communication between the user and NAiSE’s customer support team takes place through a direct, automated ticketing system. This system ensures timely responses based on the support model the company has chosen. Whether a company requires basic assistance or round-the-clock support, the automated system guarantees that the appropriate level of service is always available.
WHITE LABEL FLEET MANAGEMENT FOR ROBOT MANUFACTURERS
In the competitive robotics manufacturing industry, providing reliable and efficient fleet management is essential for customer satisfaction. However, developing the necessary software in-house can be costly and time-consuming. To address this challenge, NAiSE offers a white-label fleet management solution—an ideal choice for companies looking to provide their clients with a comprehensive, branded fleet management system without the need for internal development.
A white-label fleet management solution allows manufacturers to offer a ready-made, customizable platform that can be branded as their own. This approach significantly reduces development time and costs, allowing manufacturers to focus on their core competencies—designing and building robots—while providing their customers with a powerful fleet management system powered by NAiSE’s proven technology.