CONTINENTAL: NAISE SOLUTION IN INGOLSTADT, GERMANY
05.02.2025 | naise.eu
A COMPREHENSIVE USE CASE
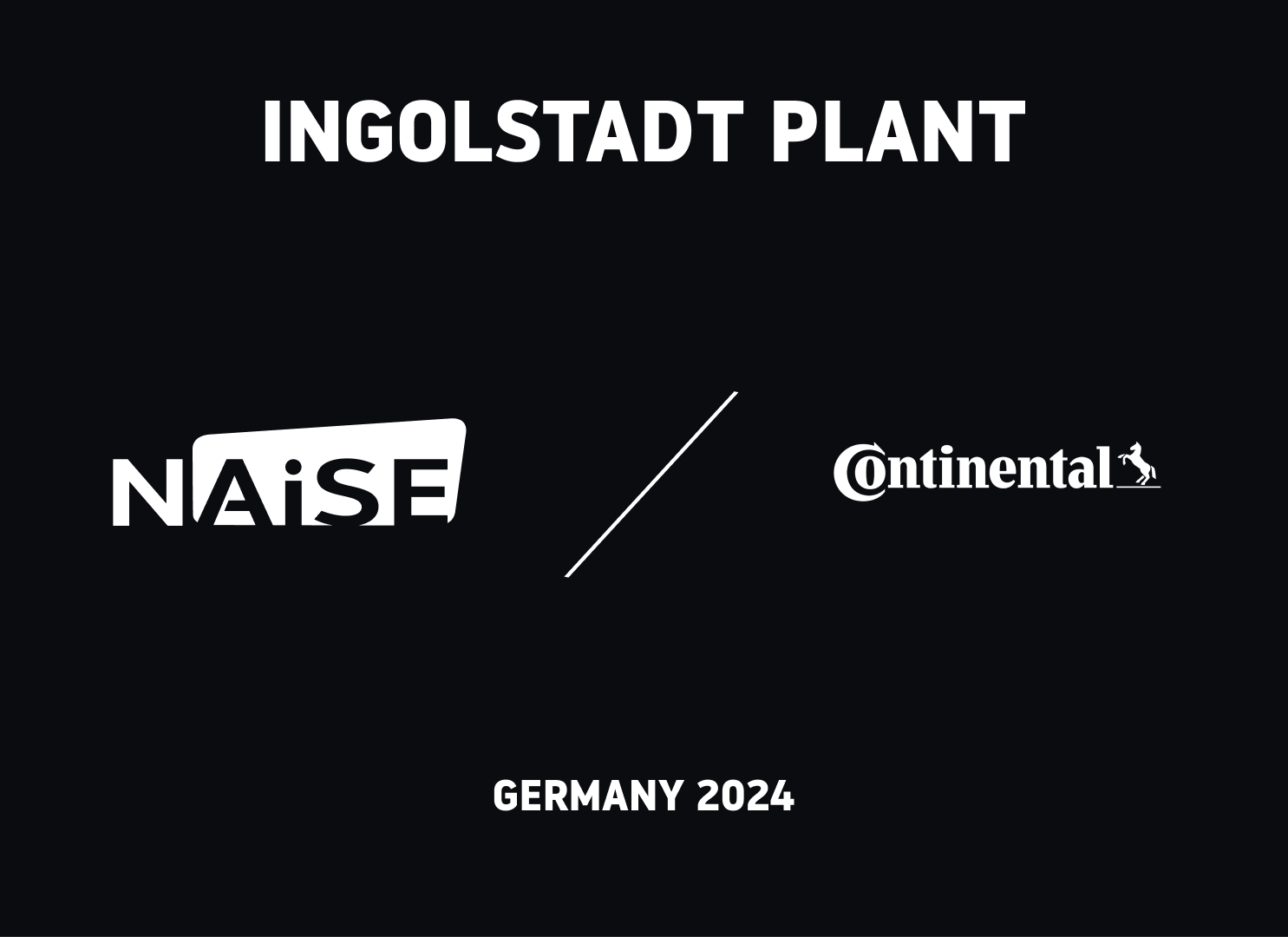
DIGITALIZATION AND AUTOMATION IN AUTOMOTIVE MANUFACTURING
Imagine a bustling factory floor where the sound of machines fills the air, and workers are constantly on the move, ensuring that each component of a complex product is perfectly assembled. Despite the best efforts of a dedicated team, minor delays can potentially lead to production bottlenecks in following production processes. Slight offsets could lead to delays, reduced productivity, and increased operational costs.
Now, envision a plant where these challenges are not just already managed properly but will be effectively eliminated in the near future. Continental’s Ingolstadt plant in Bavaria, Germany, stands as a testament to how innovation is transforming industrial operations. While not a direct pilot plant, its activities align with the broader goals of the DIAZI project – short for “Digitalization of the Industrialization Process in the Automotive and Supplier Industries” (Digitalisierung des Industrialisierungsprozesses in der Automobil- und Zuliefererindustrie). This three-year initiative aims to digitize production processes through advanced digital planning, simulation, and operation of production lines. The plant’s integration of these cutting-edge concepts reflects the DIAZI project’s vision, driving significant advancements in automotive manufacturing.
This production plant is one of over 505 Continental locations worldwide. It offers a wide range of entry and development opportunities for all career levels, fostering a highly innovative and diverse work environment. Given the critical role of PCBs, the plant in Ingolstadt has embraced cutting-edge automation technologies to streamline production and enhance efficiency. At the core of this transformation is the implementation of the NAiSE Intralogistics Platform. This article explores how NAiSE products are set to revolutionize the facility’s automation, material flow, and overall operational efficiency, addressing the common industry challenge of managing complex production processes effectively.
By tackling these challenges head-on, Continental’s Ingolstadt plant not only leads in technological advancements but also sets a new industry standard. Join us as we delve into the transformative impact of NAiSE Intralogistics Platform on the plant’s operations and discover how this facility is redefining efficiency in the modern production landscape.
ENHANCING EFFICIENCY WITH MULTI-LEVEL INTEGRATION AND PRECISION
At Continental’s Ingolstadt plant, efficient material flow and precise coordination are paramount. The facility spans multiple floors, each uniquely represented in a comprehensive 3D model within the NAiSE Intralogistics Platform, thus having a multi-leveled integration capability. The software provides a multi-level map that offers a clear, real-time view of all three production areas, creating transparency and control over the whole building. Our advanced software orchestrates the seamless movement of materials across various areas, including the warehouse, production floors, and storage units, ensuring optimal efficiency and adherence to stringent standards. For instance, the production areas, known for their rigorous cleanliness requirements, are managed with meticulous care, contrasting with the dustier environment of the warehouse. This stark difference necessitates precise and cautious handling of materials to prevent contamination and ensure quality.
Through this sophisticated integration, Continental’s Ingolstadt plant not only maintains high standards of cleanliness and efficiency but also sets a benchmark for modern industrial operations. The NAiSE Intralogistics Platform’s ability to manage multi-level operations and provide comprehensive oversight is a game-changer, driving the plant toward unprecedented levels of productivity and reliability.
SEAMLESS WORKFLOW INTEGRATION: CONNECTING AMRs, TUGGER TRAINS, AND HUMAN OPERATORS
The automation system at the Ingolstadt plant involves several key participants, including:
- – 13 non-VDA 5050 Automated Mobile Robots (AMRs)
- – 10 tugger trains
- – Forklifts
- – Human operators
- – and in the future 7 VDA 5050 Mobile Transport Robot
These participants are integrated into a seamless workflow, facilitated by the NAiSE Intralogistics Platform. The software ensures efficient communication and coordination among all participants, regardless of the manufacturer or communication standard.
MATERIAL FLOW FROM AUTOSTORE TO PRODUCTION WITH SMART AUTOMATION
The material flow process begins in the automated storage (AutoStore) system connected to the facility’s ERP system, enabling real-time tracking of components needed for the production and inventory levels. When a production order is placed, the storage unit triggers specific scripts communicated to the NAiSE Order Manager via MQTT, REST communication protocols, or messages generated manually via a GUI by human operators. When the production requires a specific component, the order is sent from ERP to the AutoStore. AutoStore prepares the material, places it in a box, and triggers a script that sends information to the NAiSE Order Manager, indicating that the material is ready. NAiSE Intralogistics Platform then uses smart decision-making to select the nearest available AMR to transport the box to the production area. This process is managed via MQTT communication protocol, ensuring seamless information flow from ERP to the storage unit, and then to NAiSE software. Once an AMR receives the order, it begins the delivery process. However, the path from storage to production includes navigating through doors and interacting with tugger trains.
NAiSE Intralogistics Platform excels in fleet, order and traffic management, independent of how orders are triggered or communicated, showcasing its manufacturer and communication standard independence. In the production process, non-VDA 5050 AMRs can also transport empty boxes back to storage, necessitating frequent interactions with human operators. Human operators load empty boxes onto the robots, updating their status in the NAiSE Intralogistics Platform to ensure proper routing.
OPTIMIZING MATERIAL TRANSPORTATION WITH LOCALIZATION AND TRAFFIC MANAGEMENT
The Ingolstadt facility utilizes a modular assembly kit to transport boxes between different floors. This system consists of rails installed throughout the building, enabling efficient vertical and horizontal transportation of materials. This seamless connectivity ensures materials move efficiently across various production stages. Human operators can interact with the system by manually scanning and moving boxes, which will lead to updating their status in the software and ensuring that materials are correctly routed.
Inside of this plant, NAiSE has implemented localization technology using Real-Time Location Systems (RTLS) with tags for tracking tugger trains and forklifts. This technology provides precise position data, which is crucial for triggering specific rules and facilitating smooth communication between robots and manually driven vehicles. The localization system ensures that all participants are aware of each other’s positions, preventing collisions and optimizing material flow. Furthermore, traffic management within the facility is enhanced with the addition of traffic lights and “STOP” signs, similar to real-world traffic systems. These enhancements ensure that robots and manually driven vehicles adhere to traffic rules, improving safety and coordination. The facility has also integrated fire alarm systems within the NAiSE Intralogistics Platform. In the event of a fire alarm, the software notifies robots to stop all the operations, preventing conflicts with human evacuation procedures.
REAL-TIME NOTIFICATIONS AND ISSUE RESOLUTION FOR UNINTERRUPTED OPERATIONS
The NAiSE Intralogistics Platform features a comprehensive notification system that provides real-time status updates for all participants in the material flow process. Thanks to different visual representations of updated information at any time, operators are able to quickly identify and address any issues. In the event of a sudden and unplanned stop of one of the AGVs, the software automatically sends information to the personnel responsible for managing and overseeing this Continental plant. This way, they are alerted that the robot has encountered an obstacle it cannot resolve without human assistance.
EXPANDING ROBOT FLEET WITH SEAMLESS MULTI-INTERFACE INTEGRATION
Looking ahead, the Ingolstadt plant plans to integrate a second robot manufacturer, namely a mobile transport robot using VDA 5050 standardization, to expand its mobile robot fleet and to execute the same tasks that the existing robots have. This integration will involve combining two different robot interfaces (VDA 5050 and non-VDA 5050) into a material flow environment. Our NAiSE Intralogistics Platform, will enable seamless collaboration, task execution and navigation within the facility, further enhancing efficiency and productivity.
A SUCCESS STORY OF INNOVATION AND COLLABORATION: NAiSE’S IMPACT AT THE INGOLSTADT PLANT
“My first Contact with NAiSE was in March 2020 and since then we have achieved a lot. When we started our collaboration, it was planned as a pilot and now the Intralogistics Platform from NAiSE is the official released tool for fleet, traffic and order management and intralogistics in our company and many more plants are using the software every day.
Without using the platform, it would be very difficult to use different AMR/AMR suppliers in one plant and also the traffic management between autonomous and manual driven vehicles would be hard to realize. But with NAiSE the implementation of different suppliers in the same area is possible and makes our traffic much more efficient and increases safety.
Another great benefit is the MQTT Interface. Therefore, the communication with external hardware like I/O-devices is very lean and easy. We’re using these MQTT publishes for example to control a traffic light in narrow areas when an aAGV is inside or even to make the escape routes in case of a fire alarm safer for pedestrians. Another use case we implemented is opening our gates via geofence zones. With this solution we reduced the transport time in our ground floor about 15-20% which helped us a lot to make the process even more efficient.
So, to summarize the collaboration is a big success and we’re still looking for new benefits and use cases to implement together.”, concluded Mr. Benedikt Branner, Smart Factory Engineer / Project Manager, Plant Ingolstadt
The implementation of the NAiSE Intralogistics Platform at the Ingolstadt plant represents a significant advancement in industrial automation and material flow management. By integrating various systems and ensuring seamless communication between different participants, the software enhances efficiency and productivity. These efforts align with broader digitalization initiatives like the DIAZI project, which supports the transformation of production processes across the automotive and supplier industries.
The facility’s commitment to continuous innovation and expansion underscores the pivotal role of NAiSE in driving advancements in automation technology. As the plant evolves, with digitalization efforts continuing to unfold, NAiSE will remain at the forefront, enabling new levels of operational excellence and technological integration.