DIGITALIZING AUTOMOTIVE PRODUCTION: THE DIAZI PROJECT
25.09.2024 | naise.eu
TRANSFORMING AUTOMOTIVE PRODUCTION THROUGH DIGITALIZATION AND INNOVATION
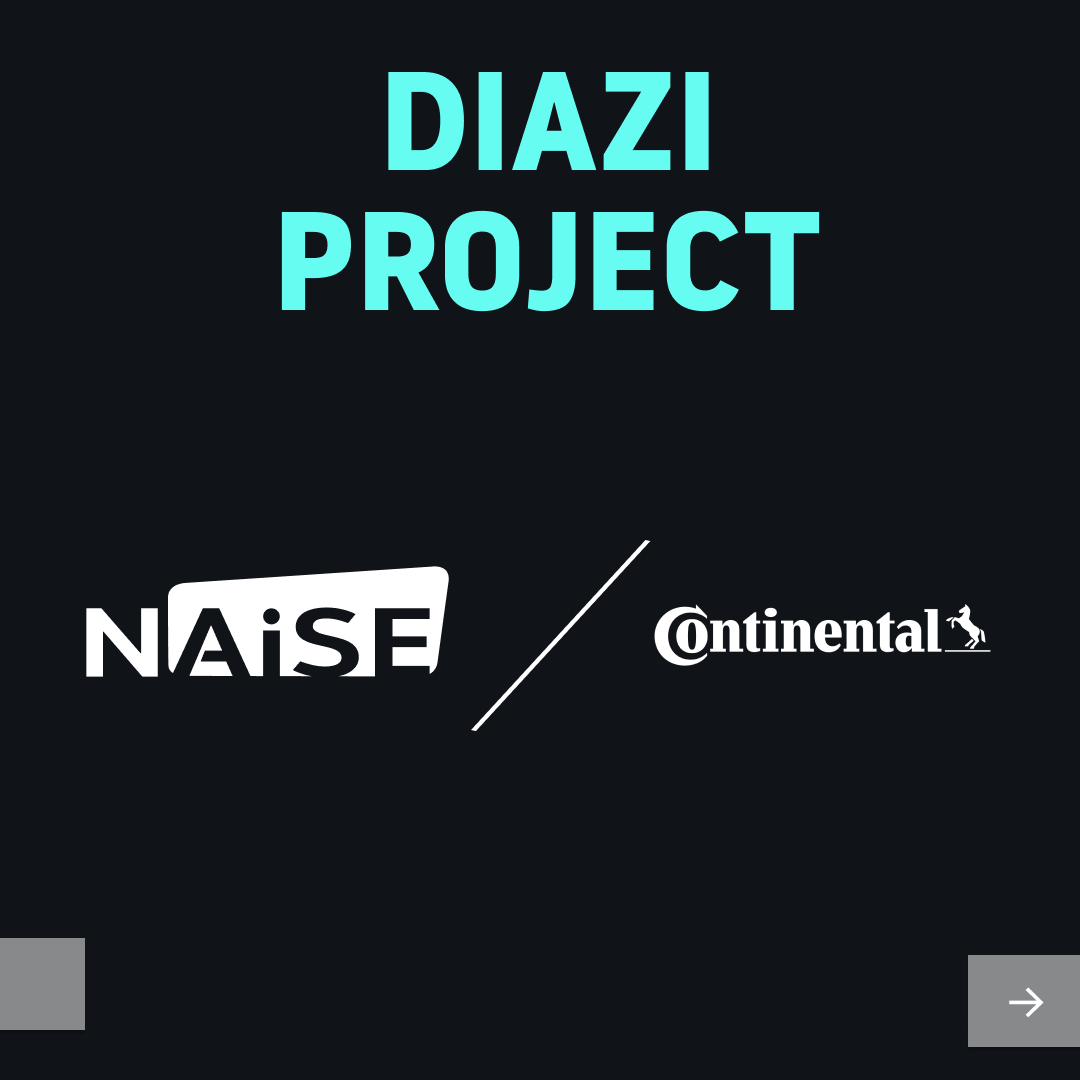
NAiSE’S ROLE IN SHAPING THE FUTURE OF SMART MANUFACTURING
Continental is leading the change toward digitalizing the entire production process for automotive components through the groundbreaking DIAZI project. This ambitious endeavor, funded by the German Federal Ministry for Economic Affairs and Climate Action, brings together a consortium of seven esteemed IT and process optimization companies, universities, and specialized start-ups, and notably, our company NAiSE. As a key partner in the project, NAiSE leads with its expertise and innovative solutions to the collaborative effort aimed at digitalizing automotive production through the DIAZI initiative. Furthermore, Continental’s User Experience business area spearheads project management, steering efforts the digitalization of industrialization processes in automotive industries.
The DIAZI project, acronymizing ” Digitalization of the Industrialization Process in the Automotive and Supplier Industries” spans a three-year timeline, with a primary objective of transferring production plants into the digital world. This visionary initiative promises to revolutionize the automotive manufacturing landscape by introducing digital planning, simulation, and operation of production lines. The results of this project will be tested and proven in Continental’s plants across Europe, for example the company’s Megafactories Brandys and Novi Sad. The aim? To increase efficiency, flexibility, sustainability, and cost-effectiveness while ensuring modern automotive plants remain agile amidst faster development cycles, complex supply chains, and evolving customer demands.
The aims of the DIAZI project resonate deeply with NAiSE’s core values and mission. With shared commitment to enhancing efficiency, flexibility, sustainability, and cost-effectiveness in automotive plants, our collaboration is more than just a project-based partnership – it’s a shared journey towards a future where innovation and progress intersect seamlessly. Thus, being such an important partner in this project, our role is clear: to leverage our expertise in Route Optimization, Traffic Analysis, Order Management, and Intelligent Battery Management, to propel the automotive production evolution where technology is used not just for efficiency, but also to create a more responsible, human-centered, and sustainable industrial future.
As we embark on this collaborative journey with the DIAZI project, the road ahead is rich with possibilities. Stay tuned as we delve deeper into how NAiSE’s contributions will shape the future of automotive production, revolutionizing the way we drive, innovate, and thrive in a digitally connected world.
INTELLIGENT BATTERY MANAGEMENT
At the forefront of innovation within the DIAZI project is the integration of Intelligent Battery Management systems. Through an optimization algorithm, we mark a significant stride towards optimized and automated operations within the intralogistics domain. Imagine fleets of Automated Guided Vehicles (AGVs) and Autonomous Mobile Robots (AMRs) seamlessly navigating through warehouses, tirelessly executing tasks with precision. Behind this choreographed ballet lies a sophisticated orchestration of AI-driven algorithms, carefully optimizing charging schedules to ensure maximum productivity.
The core innovation of Intelligent Battery Management lies in its predictive capability. By forecasting battery levels with precision, the system orchestrates power management, ensuring each robot is primed and ready for optimal performance. This predictive power empowers operators to detect potential battery decrease, strategically allocating resources to sustain operational continuity.
But how is such foresight achieved? Through bespoke AI models that are generalized to predict each robot without having to work separately. These models, like digital guardians, continuously monitor battery levels, learn their patterns and behaviors, and by leveraging sophisticated feature engineering techniques they are able to distill meaningful insights. With machine learning models finely tuned, the journey of training and validation starts, sharpening algorithms to perfection.
Our strength lies in the generality of our approach as we’ve developed a model capable of predicting the behavior of any robot in our fleet without the need for individualized customization. Rather than creating digital twins for each unit, our focus is on simulating battery behavior to generate extensive data for training the AI model. This approach eliminates the need for bespoke models for each robot and allows us to efficiently utilize a single model across different units.
Yet, the true test lies in real-world application. As AI algorithms interface with tangible robots, they undergo rigorous testing, learning the nuances of behavior and adapting in real-time. This symbiotic relationship between AI and machinery heralds a new era of intralogistics, where intelligent decision-making becomes the cornerstone of efficiency.
In the grand world of intralogistics, AI emerges not merely as a tool but as a beacon of innovation. With Intelligent Battery Management systems at its core, the automotive industry navigates towards a future where efficiency knows no bounds, and every robot dances in harmony with the rhythm of progress.
Our accomplishments thus far in implementing Intelligent Battery Management speak volumes. By seamlessly integrating AI-driven algorithms, we have unlocked unprecedented efficiencies, ensuring our fleet of robots operates at peak performance levels, contributing to the broader vision of sustainable mobility and digitalized automotive production. As the DIAZI project continues to unfold, our commitment remains unwavering: to drive innovation, enhance efficiency, and lead the automotive industry into a brighter, sustainable and more digitally enabled future.