USE CASE: AUTOMATED LOGISTICS AND TRAFFIC MANAGEMENT SYSTEM AT CONTINENTAL PLANT, BRANDYS, CZECH REPUBLIC
13.09.2024 | naise.eu
INNOVATIVE SOLUTIONS FOR A DIGITAL FUTURE IN MANUFACTURING
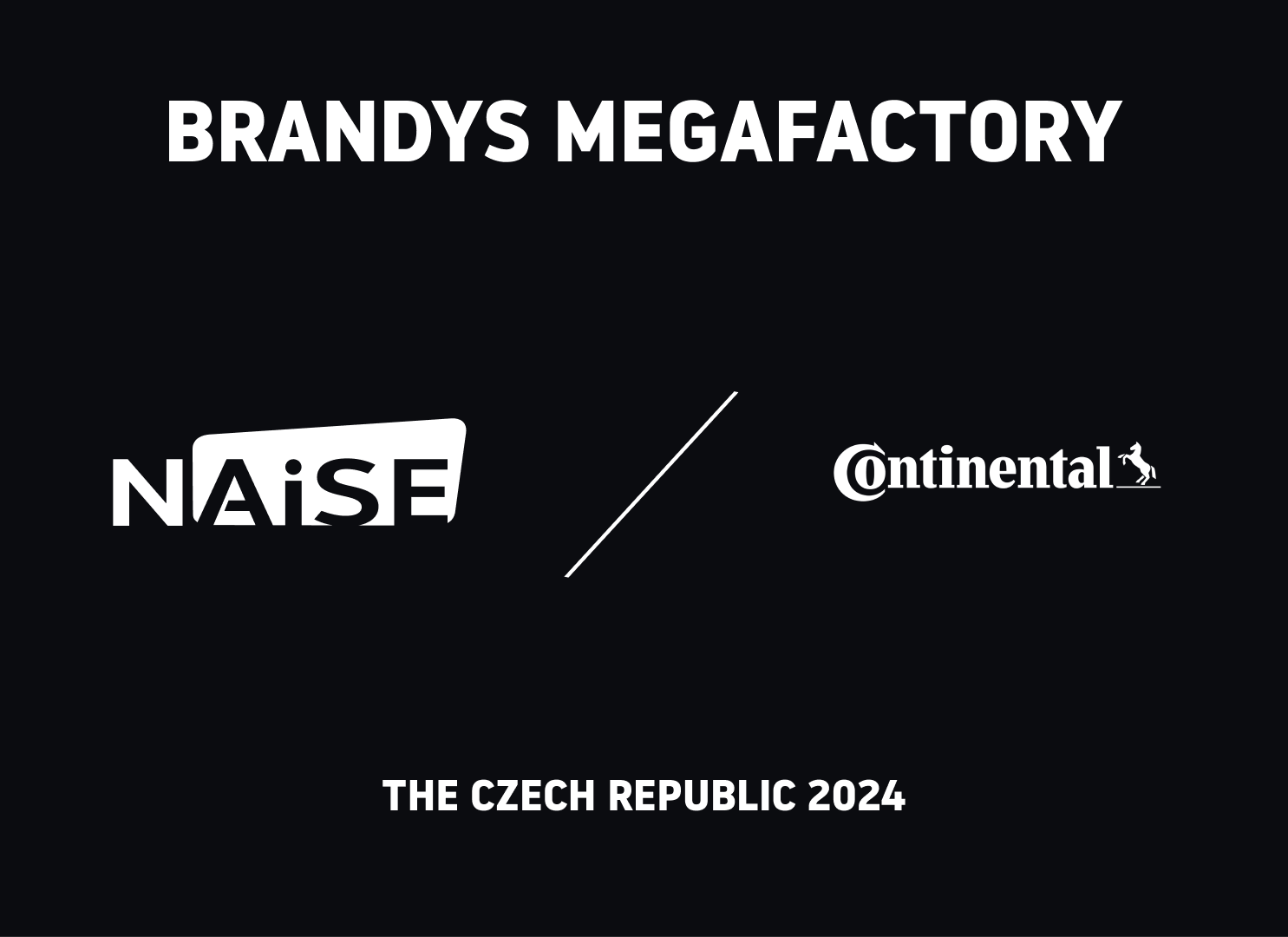
SETTING THE STAGE
Continental’s plant in Brandys, Czech Republic, stands as a testament to the country’s advancing innovation in industrial automation. The location is part of the DIAZI-project, which is also funded by the German Federal Ministry of Economics and Technology. Goal of the project, in which NAiSE and Continental are closely working together to transfer production plants into the digital world to enable new production lines being planned, simulated and operated digitally which leads to increased efficiency, flexibility and cost-effectiveness. This allows to keep pace with faster development cycles, complex supply chains and changing customer requirements. Over recent years, the Czech Republic has been evolving in optimizing warehouse operations through automation and cutting-edge technologies. As stated in a report by the World Economic Forum, “Technology adoption will remain a key driver of business transformation in the next five years.” Further implementation of such Technology is enabling Continental to expand and safely mix its fleets with better and more cost-effective AMR as the market has been rapidly evolving in the last years.
At the heart of this revolution is NAiSE, a long-standing partner of Continental. Our collaboration with Continental spans multiple plants, including the state-of-the-art facility in Brandys, where we’ve implemented advanced solutions to enhance operational efficiency and productivity.
ADDRESSING COMPLEXITY IN WAREHOUSE AUTOMATION
Integrating robots from various manufacturers within a single facility presents significant challenge, particularly when these robots operate on different interfaces such as VDA5050 standard other native (non-VDA5050) interfaces, and manually driven vehicles – all in the same facility. The Continental plant in Brandys faced this exact challenge. We approached this complexity by deploying our advanced software and Traffic Management, designed to connect the warehouses and production halls seamlessly.
USE CASE PARTICIPANTS
The Brandys plant employs a diverse array of autonomous solutions to handle its complex material flow requirements. This includes two types of AMR with native interfaces (non-VDA5050). With a total of three robots actively operating in the facility, one intended for the transport of pallets, while the other two are intended for the transport of boxes. These robots are crucial for maintaining the efficiency and reliability of material handling processes.
Additionally, manually driven vehicles, in this case tugger trains, are integral to the plant’s operations, interacting seamlessly with autonomous robots to ensure transparent, flexible and simple material flow.
Managing this combination of autonomous robots and manually driven vehicles requires a sophisticated system capable of integrating diverse technologies and workflows. Our solution effectively bridges this gap, ensuring that all participants in the material flow process can operate in harmony, thus expecting an enhancement of the overall productivity of the plant.
PROCESS INTEGRATION
NAiSE Software ensures efficient connection and coordination of the various processes occurring in the warehouses and production halls. Here’s a detailed breakdown of how this integration works:
– Production Hall: AMRs are equipped with docking stations that are integrated with a storage system. These robots are tasked with transporting boxes within the production hall, ensuring that materials are moved to the correct locations efficiently. The AMRs dock, load or unload materials, and navigate through the hall to their designated spots.
– Warehouse: AMR handles the transportation of pallets. This AMR picks up pallets from one production hall and bring them to another production hall, ensuring a continuous material flow between production areas. After delivering the full pallets, AMR takes empty pallets from the production hall and brings them back to the warehouse, optimizing the utilization of storage space and ensuring that materials are always available where needed.
– Tugger Train: Manually driven tugger trains play a critical role in maintaining the continuous supply of materials. These trains transport pallets or boxes from the storage system to the production hall and then to the warehouse. This ensures that materials are consistently supplied to where they are needed most and that storage areas are efficiently utilized.
This integration demonstrates the seamless operation of both manually driven vehicles and autonomous robots within our software framework. The ability to coordinate these diverse elements is intended to ensure that materials flow smoothly and efficiently through the facility, reducing delays and increasing productivity.
AUTOMATION OF TUGGER TRAINS
Our solution includes the NAiSE localization system (Real-Time Localization Systems – RTLS) to accurately track the positions of manually driven vehicles within the facility. This system continuously collects real-time data on vehicle locations and movements, transmitting this information to our software. This integration enables effective coordination and communication between different types of vehicles, ensuring smooth operation across the entire plant. By harmonizing the activities of various autonomous and manual vehicles, we significantly reduce operational downtime and enhance overall efficiency.
Our implementation of RTLS at Continentals’ Brandys plant is crucial for the precise positioning and tracking of tugger trains. The real-time localization data provided by RTLS allows hall and production managers to monitor the exact location of tugger trains at any given moment. To achieve this level of precision, we installed 54 anchors and 8 gateways strategically throughout the facility.
In terms of industrial automation, we implemented the integration of door control systems. When AMRs approach these automated doors, they enter a custom-defined zone in NAiSE software. Upon entering this zone, the doors open automatically, allowing for uninterrupted movement between different areas of the plant. This automation is essential for maintaining the flow of materials and ensuring the efficiency of the entire operation.
Additionally, we have installed projectors connected to narrow zones defined in NAiSE software. When a robot enters a designated area, the projectors display a corresponding sign on the floor (for example sign “STOP”), signaling other participants to wait until previous order becomes done. This visual cue is set to enhance safety and ensure that robots and humans can operate within the same space without accidents or disruptions.
FUTURE GOALS
Our vision for the future is to achieve a fully integrated environment where all participants—robots and manually driven vehicles—can operate seamlessly across ALL areas, including warehouses, production halls, and storage systems, without any restrictions. This goal aims to further enhance efficiency and productivity across the entire facility. By continually advancing our technology and refining our integration strategies, we aim to create an optimized and fully automated environment that sets new standards for warehouse operations and material handling. Continental’s Brandys plant is also the environment in which the latest achievements of the DIAZI project, funded by the German Federal Ministry of Economics and Technology, are being tested and implemented.
NAiSE: Link
Continental: Link
DIAZI: Link