THE POWER OF AGVs AND AMRs
15.07.2024 | naise.eu
THE FUTURE OF INDUSTRY
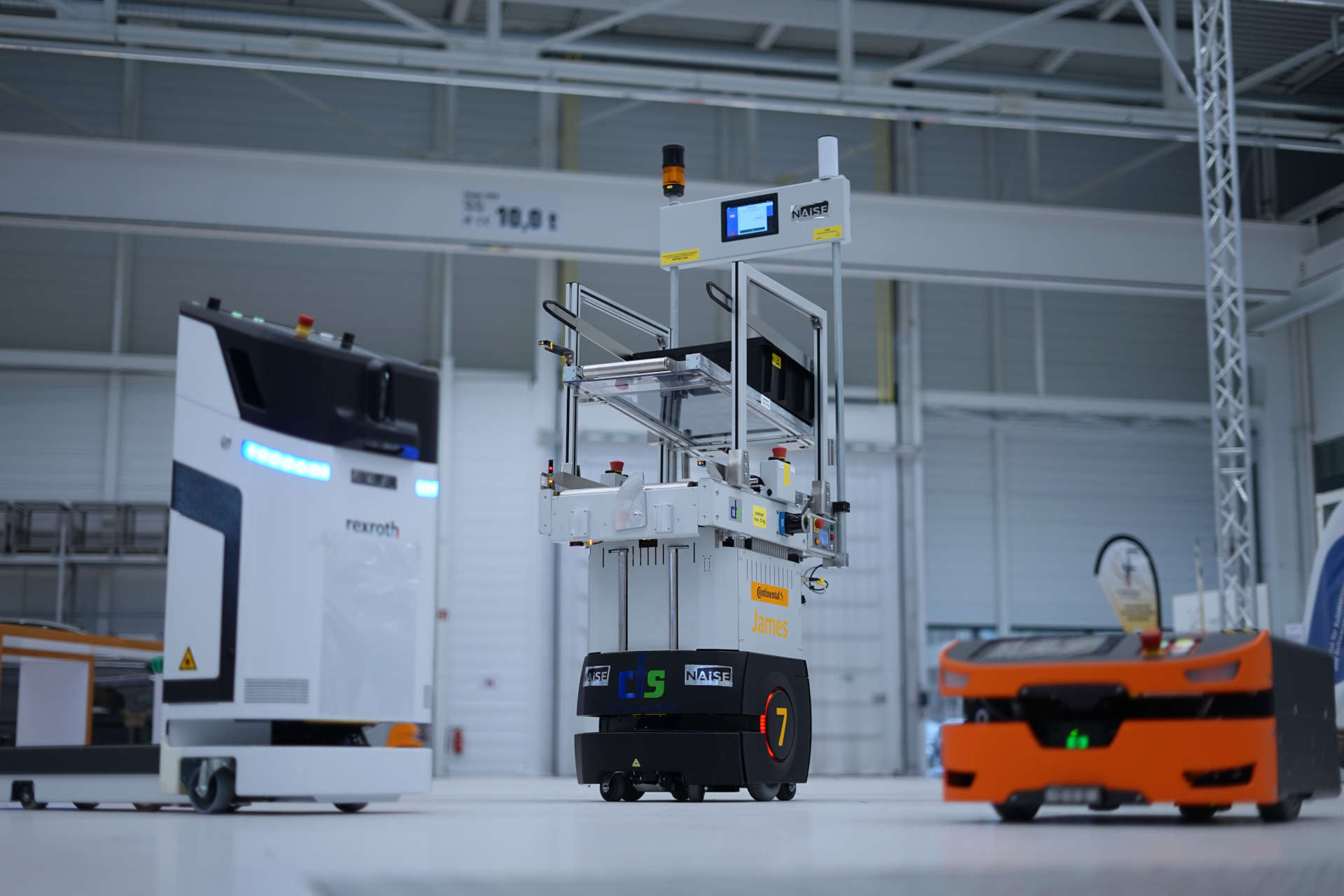
THE EVOLUTION OF MATERIAL HANDLING
Throughout history, factories have depended on human labor to handle material transportation, often requiring workers to perform repetitive and physically demanding tasks, but with the dawn of industrialization, innovations like conveyor belts and early automation provided some relief, but the true transformation is happening now. To stay competitive, companies must continuously improve their processes to meet increasing demands and as market competition also enhances their processes, embracing automation becomes essential for all to keep pace with evolving market requirements.
Picture a modern factory where materials glide effortlessly from one station to another without human intervention; this isn’t a scene from a sci-fi movie – it’s the present reality thanks to Automated Guided Vehicles (AGVs) and Autonomous Mobile Robots (AMRs). These robots use cutting-edge technology to navigate factory floors, ensuring efficient and safe material flow. Historically, workers spent countless hours moving items, which was both time-consuming and prone to error. The introduction of AGVs and AMRs revolutionizes this process by automating material transport, reducing the need for human involvement in monotonous tasks. This shift allows workers to focus on more valuable and engaging activities, boosting overall productivity and job satisfaction.
The evolution of material handling in factories, from manual labor to advanced robotics, marks a significant milestone in industrial development. AGVs and AMRs are not just improving efficiency; they are reshaping the way factories operate, creating a future where humans and robots work side by side in harmony. In this new era, automation is not about replacing humans but about enhancing their roles, leading to safer, more efficient, and more innovative workplaces.
PRIORITIZING SAFETY IN INDUSTRIAL SETTINGS
Safety is the foundation of any successful business. Companies need to grow while keeping their employees safe. A study from Finland found that human error causes 84 to 95% of serious industrial accidents (Salminen & Tallberg, 1996). This shows that automation is not just about improving productivity; it’s also about making the workplace safer. Modern automated systems are equipped with advanced safety sensors to understand their environment and react accordingly — either stopping, changing direction, or adapting to prevent accidents. These sensors can detect obstacles, identify changes in the surroundings, and ensure that the machinery operates within safe parameters. This significantly reduces the risk of accidents that are common with manual labor.
In intralogistics, human errors like collisions, insufficient experience, and lack of transparency can lead to significant safety issues. Automation mitigates these risks by enhancing precision and reliability. Additionally, automated systems can be integrated with real-time monitoring and control systems that provide continuous feedback and analytics. This helps in identifying potential hazards before they become critical, ensuring proactive maintenance and quick response to any issues that arise.
Embracing automation not only boosts productivity but also transforms workplace safety. By leveraging advanced safety sensors, reducing human error, and minimizing physical strain, companies can create a safer and more efficient working environment.
ENHANCING MATERIAL HANDLING WITH AGVs AND AMRs: THE EVOLUTION OF AUTONOMOUS TRANSPORT
It may be surprising to learn that Automated Guided Vehicles (AGVs) have been around since the 1950s. Initially introduced by Barrett Electronics of Northbrook, Illinois, the first AGVs were simple towing machines that followed a wire embedded in the floor. This technology marked the beginning of a new era in automated transport, paving the way for the sophisticated AGVs we see today.
Over the decades, AGVs have evolved significantly. From basic towing machines, they transformed into high-tech systems that follow invisible UV markers on the floor, as first implemented in the Willis Tower in Chicago, Illinois, for mail delivery. Today, AGVs are at the forefront of automation in warehouses and factories, playing a critical role in improving material flow visibility and reducing downtime.
AGVs, or Automated Guided Vehicles, are load carriers that transport materials within a facility without the need for an onboard operator. They utilize advanced software and guidance systems to move loads with precision, maximizing efficiency and reliability. By automating consistent and recurring transport tasks, AGVs allow human workers to focus on more complex and specialized tasks, enhancing overall productivity.
The integration of AGVs into material handling operations provides several benefits. These vehicles manage repetitive tasks typically handled by forklift operators, reducing the risk of human error and physical strain. AGVs help to streamline operations, reduce costs, and create a safer working environment. While AGVs can operate independently, they are also designed to work seamlessly alongside manual trucks and pedestrians in mixed operations. Many AGVs offer manual operation options, adding versatility and making them a valuable asset for warehouse managers seeking equipment that can perform multiple tasks efficiently.
On the other hand, Autonomous Mobile Robots (AMRs) also automate material transport but work differently from AGVs. AMRs use advanced software and sensors to create maps of their environment, allowing them to navigate freely and adapt to changes.
It is not widely known that during World War II, the first mobile robots emerged as flying bombs, thanks to advances in computer science and cybernetics. These early robots, like the V1 and V2 rockets, had crude ‘autopilot’ and automatic detonation systems, making them the predecessors of modern cruise missiles. Fast forward to today, AMRs use cameras, sensors, and laser scanners to understand their surroundings and move around obstacles on their own.
Nowadays, AMRs are highly versatile and can be used for a variety of tasks, including transporting goods, picking and placing items, and even conducting inspections. Their ability to work autonomously and adapt to their environment makes them an invaluable asset in industries seeking to improve efficiency and reduce labor costs. Furthermore, AMRs can work collaboratively with human workers, enhancing productivity by taking over repetitive and physically demanding tasks, thereby reducing the risk of injuries and allowing human workers to focus on more complex and value-added activities.
In addition to their operational benefits, AMRs can also provide valuable data insights through their integrated sensors and software systems. This data can be used to optimize workflows, track inventory in real-time, and improve overall operational efficiency.
AGV VS. AMR
The main difference between AGVs and AMRs is flexibility: AGVs follow fixed routes and need facility modifications, making them less adaptable and more expensive. In contrast, AMRs are highly flexible, needing only software updates to change tasks. This makes them ideal for dynamic environments. AMRs can prioritize tasks based on location and availability, providing a more agile and cost-effective solution compared to AGVs. Over time, AGVs may become a limitation due to their rigidity, while AMRs can be quickly deployed and adjusted to meet changing needs, enhancing overall efficiency.
INTRODUCING NAiSE: YOUR ULTIMATE INTRALOGISTICS SOLUTION
Now, let’s talk about how our company is taking automation to the next level with NAiSE Intralogistics Platform. One of the standout characteristics of NAiSE is its ability to seamlessly connect with any existing transport mobile robot, regardless of the manufacturer. This capability fosters collaboration between different robots, ensuring they work together efficiently. We enable robots to work together by combining different functions and capabilities from various manufacturers without interrupting the interface and hardware components of the robots. Instead, we integrate them through a streamlined software integration process.
Many manufacturers have already joined the NAiSE community, and all other AGV and AMR manufacturers can be fully integrated based on the needs of the end user. This means that businesses have access to a wider range of robots, offering more options for customization and optimization. Additionally, companies don’t need to have multiple fleet managers; they can manage everything with our all-in-one solution. NAiSE also facilitates seamless collaboration between robots, humans, and machines controlled by humans.
By using NAiSE Intralogistics Platform, businesses can improve the material flow process in which the robots operate, enhancing overall efficiency and reducing operational costs. The system reduces wait times, increases throughput, and ensures that orders are processed efficiently and accurately. Importantly, we don’t optimize the robots themselves; we improve the processes in which the robots are used, which is crucial to maintaining good relationships with robot manufacturers.
“NAiSE Compatibility” makes it easy to find the most efficient AGVs, AMRs, and navigation platforms. Being NAiSE compatible means that AGVs, AMRs, and other industrial solutions from various manufacturers can be connected with NAiSE products. This integration helps users reduce costs and streamline the process of incorporating new robots into their intralogistics operations.
Integration Level 1: This initial stage involves consulting with a technical expert from the robot manufacturer to understand the necessary interfaces for integration.
Integration Level 2: The next step includes initial software integration, testing in a cloud or docker environment, and a requirement checklist to support the robot manufacturer throughout the integration process.
Integration Level 3: The final stage involves a comprehensive testing routine, conducted either at our testing center (ARENA2036 in Stuttgart) or in the robot’s final application area.
NAiSE integrates any AGV or AMR, regardless of the interface (VDA 5050 or non-VDA 5050). Our solution ensures that AGVs and AMRs work seamlessly with workers, forklifts, and tugger trains, executing tasks together without interference.
As industries evolve, adopting AGVs and AMRs with the support of NAiSE Intralogistics Platform can significantly improve both safety and productivity. Automating repetitive and hazardous tasks creates a safer work environment and allows employees to focus on more valuable activities.
More information about integrated manufacturers: LINK